ISO 9001:2015 Quality Management Systems is the most commonly sought after certification across the ISO Standards. This standard concerns the establishment of quality management principles designed to develop and maintain higher standards for operational processes and the quality of products and services provided by an organisation to their clients and customers.
Given the process-oriented nature of this ISO standard, obtaining ISO 9001 certification naturally requires full participation from all staff and relevant stakeholders within an organisation, an a well-executed implementation plan.
At S&J Auditing & Consulting, our consultants specialise in producing tailored ISO management system for your business. Our services help deliver an ideal certification readiness plan for your organisation, ensuring that your unique business goals are taken into consideration to craft a focused quality management system that benefits both your staff and clients.
To provide insight into our processes, we’ll be outlining a step-by-step guide to achieving ISO 9001 certification for your Australian business. We’ll also be sharing some expert tips on how to streamline your certification process and ensure that you can maintain your quality management system effectively.
How to Achieve ISO 9001 Certification: A Step-By-Step Guide
Conduct a Gap Analysis
Initial Assessment
A gap analysis acts as an initial review of your organisation’s current quality management system against the ISO 9001 standard requirements. By identifying ‘gaps’ between existing systems and the quality management systems you’re looking to integrate, we can develop a tailored implementation plan and proceed to Step 2 of this ISO 9001 certification process.
Consultant Collaboration
Gap analyses are best conducted with an ISO 9001 consultant to ensure an effective and streamlined approach. Begin by providing your consultant with view-only access to any documentation supporting your current quality management system (i.e. quality documentation, forms, job descriptions etc.). Your consultant can familiarise themselves with these documents to then begin preliminary independent identification of any potential gaps in comparison to ISO 9001 requirements.
Stakeholder Communication
Next, your consultant must verify these potential gaps by discussing with relevant parties. Your consultant should communicate with all the staff members covering both managerial and operational aspects of your business (including department heads, decision makers, and any Work Health & Safety/Environmental/Compliance officers). Communications with staff can aid consultants in not only confirming gaps, but also understanding your organisation’s goals and objectives for attaining ISO 9001 certification in context.
Final Report & Recommendations
Upon completion of the gap analysis, your consultant will provide a report of corrective actions that must be met to ensure certification readiness for your organisation. Our consultants will ensure that this report provides actionable improvement recommendations that are unique to your organisation. This tailored report will then provide the blueprint for your process approach to attaining ISO 9001 certification.
Key Actions in This Step:
- Review current quality management system
- Share documentation with consultant
- Engage with key stakeholders
- Receive and review gap analysis report
Develop a Project Plan for Implementation
Essential Plan Components
Once your ‘Required Improvements’ have been provided, organisations can then develop a project plan for implementation. This plan should include:
- Implementation corrective actions based on the results of the gap analysis
- An implementation timeline with identified milestones
- A list of resources that will be allocated to support implementation
Resource Planning
Resource allocations for implementation can include the development of new documentation and processes, and outlines of new roles and responsibilities for staff that are involved in the addressing of corrective actions (i.e. safety officers, internal auditors, etc.).
Key Actions in This Step:
- Create detailed implementation timeline
- Identify required resources
- Define roles and responsibilities
- Establish project milestones
Implement Necessary Changes and Documentation
Initial Implementation
Once the corrective actions are approved, organisations must then lay the foundation for all required improvements. This can be completed by working with our consultants and creating or updating documentation to ensure they’re in accordance with ISO 9001 requirements.
Employee Training & Integration
Updating documentation can also support employee training initiatives required for implementation. Training employees on new procedures/processes can help improve the likelihood of adoption and integration for new/updated processes that align with ISO 9001 certification requirements.
Keep in mind: Accurate and organised record-keeping is the backbone of certification readiness for all businesses. To ensure that your Certification audit is successful, ensure that your organisation develops and maintains record-keeping systems alongside customer-facing and other operational systems and processes.
Key Actions in This Step:
- Review and implement corrective actions
- Update existing documentation
- Conduct employee training sessions
- Establish record-keeping systems
Conduct Internal Audits
Internal Audit Process
Upon completion of your implementation timeline and sign off that your organisation has met all the objectives and goals outlined in your implementation action plan, it’s finally time to confirm implementation of ISO 9001 processes by conducting an internal audit. In simple terms, an internal audit serves as an independent inspection to effectively identify any remaining non-conformities or to ensure successful implementation of your ISO 9001 systems. Thorough internal audits are mandatory prior to your external Certification audit, and as such, external auditors will request your internal audit report to verify ISO compliance.
Pro tip: One of the most commonly identified areas for improvement for ISO 9001 Quality management system certification is evidence of a culture that supports continual improvements. Continual improvements are a key principle of the ISO 9001 standard. As quality management systems require routine revision and updating to ensure that they stay effective, establishing your quality management systems should also include the implementation of robust monitoring and measurement systems. Encouraging staff feedback and performing regular assessments can help demonstrate that your organisation is well-equipped to make continual improvements to your ISO 9001 systems.
Key Actions in This Step:
- Complete implementation timeline
- Conduct thorough internal audit
- Document audit findings
- Implement continuous improvement measures
Schedule and Complete the Certification Audit
Preparation Phase
The final step of the process to achieving ISO 9001 certification is the scheduling and completion of an external Certification audit. This final phase involves:
- Selecting an accredited certification body (your Conformity Assessment Body)
- Establishing timelines (with external auditors and staff)
- Preparing employees and documentation for the external audit
- Outlining expectations during the audit process (including interviews and document reviews)
- Addressing any last-minute non-conformities to avoid delays with attaining ISO 9001 certification
Stage 1: Documentation Review
During Stage 1 and Stage 2 of your external audit, your auditor will evaluate the effectiveness of your implemented management systems, their ability to deliver consistent results and support your business goals, and their conformance with the ISO 9001 standard. Stage 1 consists of a thorough review of all your QMS documentation, and is typically conducted independently by the auditor either remotely or on-site in a private office.
Stage 2: On-site Assessment
Contrastingly, Stage 2 is conducted on-site complete with interviews of staff and stakeholders. Stage 2 is designed to be an active audit of your work processes, with external auditors observing the ISO 9001 processes in action and ensuring the workflows align with the provided QMS documentation, and with the ISO 9001 standard.
Final Certification
If your external auditor confirms successful implementation of the QMS and conformance with the ISO 9001 standard, your organisation will be eligible to receive your ISO 9001 conformance certificate. In most cases, however, your external auditor may identify minor non-conformances that must first be corrected. In these instances, you will only need to correct these non-conformances and inform your registrar before your ISO 9001 certificate can be issued.
Key Actions in This Step:
- Select certification body
- Complete Stage 1 documentation review
- Undergo Stage 2 on-site audit
- Address any identified non-conformances
- Receive ISO 9001 certification
Tips to Expedite the ISO 9001 Certification Process
Generally, you can expect the process of attaining ISO 9001 certification (from your gap analysis to your external Certification audit) to take anywhere between 1-6 months.
If you’d like to expedite this process, it’s imperative that you develop an implementation project plan that provides a clear, linear timeline that accommodates all staff and accounts for any potential obstacles/barriers to implementation.
Here are some of the best methods for ensuring a streamlined implementation and audit process for your organisation:
1. Maintain communications with staff
Your staff have boots on the ground during the implementation process and are thus, most likely to identify any non-conformances or barriers to implementation. Communicating with staff and securing feedback regularly can aid in addressing issues proactively and as they appear.
2. Develop clear templates and checklists for staff
Providing departments with clearly actionable steps can help ensure process implementation can take place as seamlessly as possible.
3. Ensure top-level commitment
Attaining ISO 9001 certification requires full participation and involvement from all staff and stakeholders – including department leaders. If your department leaders aren’t committed to the implementation process, it may hinder integration of revised ISO processes and full implementation of your QMS. This is also the reason why our consultants at S&J also recommend dedicated ISO training initiatives for decision makers within your business.
4. Establish record-keeping processes first
Organisation is key when it comes to preparing for ISO audits. The best method a business can take to support implementation and certification is to develop a document storing and record-keeping process prior to developing any QMS documentation.
Case Study: Tyre Response Group's ISO 9001 Certification Journey
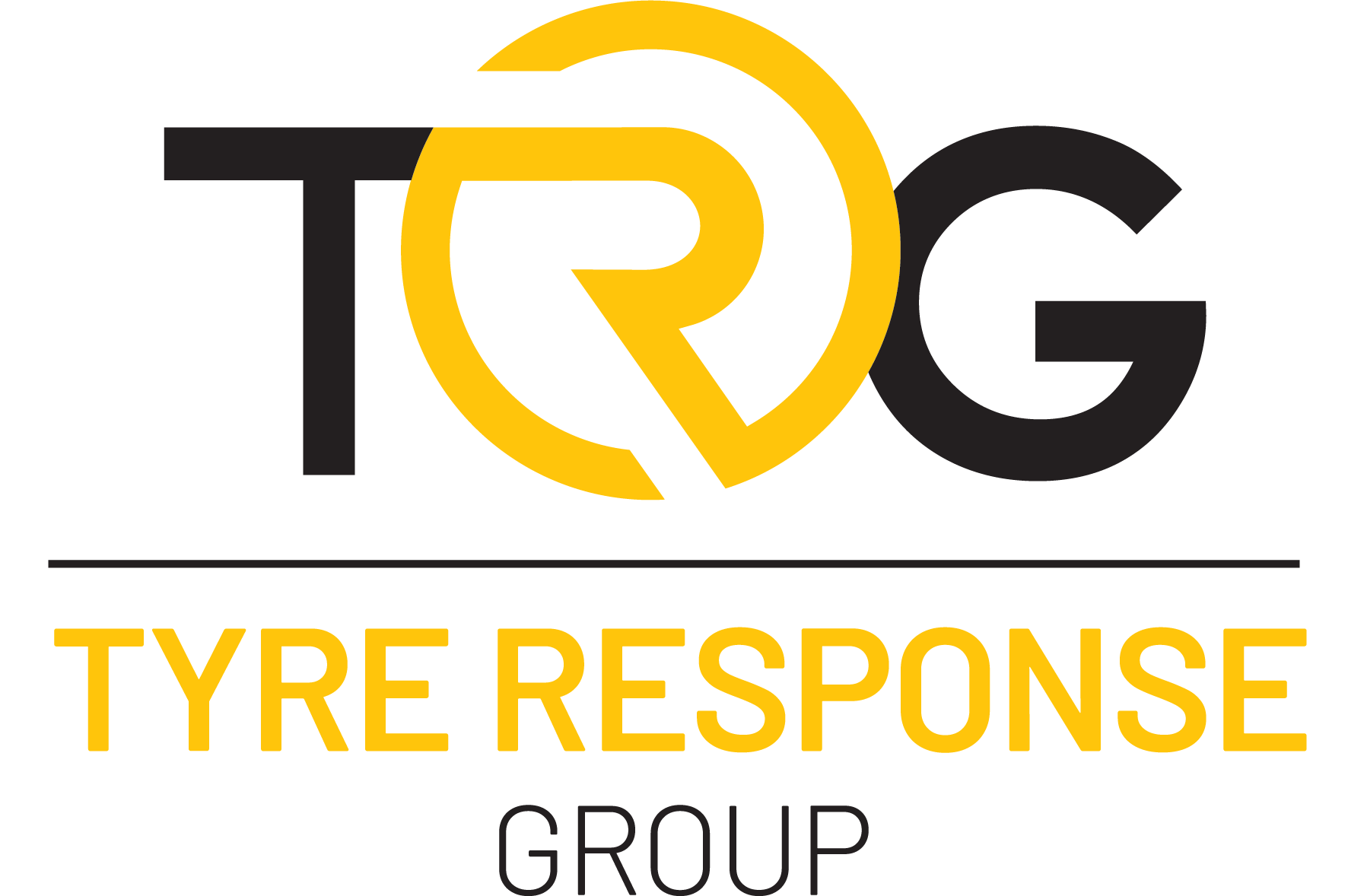
Want to see how our consultants at S&J Auditing & Consulting can support your enterprise in attaining ISO 9001 certification? Our extensive list of case studies spans a wide range of industries, with all of our clients receiving tailored business management systems that meet all required standards as well as their organisational goals.
The Challenge
Our work with Tyre Response Group showcases the level of support you can expect from our consultants during your own ISO 9001 certification process. With the support of our consultants, Tyre Response Group were able to promptly address the identified challenges in their implementation journey, including process inefficiencies and barriers to quality control.
Our Approach
By developing actionable steps to process improvements that were in alignment with ISO 9001 requirements, our consultants provided Tyre Response Group and their team with the development and documentation strategies they needed to experience a seamless implementation journey.
The Results
After successfully attaining their ISO 9001 certification, Tyre Response Group continues to utilise the support of our consultants in ensuring that their QMS continues to perform optimally, and can be continually improved in accordance with customer, staff, and stakeholder feedback.
Key Achievements:
- Increased operational efficiency
- Greater customer satisfaction
- More commercial opportunities
- Maintained firm market position
Secure ISO 9001 Certification for your Organisation with S&J
From meeting regulatory requirements, bolstering company reputations, and even just fostering a culture of quality workmanship and continual improvements, the process of achieving ISO 9001 certification is a pivotal journey for any future-oriented enterprise.
As your workflows are unique to your organisation, developing an implementation project plan that’s tailored for your business goals is essential to ensuring your ISO 9001 QMS is as impactful as possible.

ISO Consultants
If you’d like to reap all the benefits of a fully tailored ISO 9001 implementation plan, get in touch with our dedicated consultants at S&J Auditing & Consulting today.